INDUSTRY INSIGHTS
An Engineer's Guide to Choosing an Electronic Prototype House
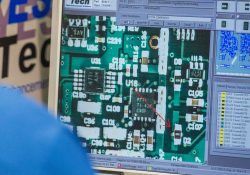
As an electrical engineer, the primary goal after the design stage is to prove the circuit concept and verify the design theories. To do this in the past, an engineer was expected to design a circuit, then get out the breadboard and wire wrap tools and build the thing. However, even when components were the size of Legos and you could actually see a resistor or cap with the naked eye, circuit construction was only manageable at best. A lot of work went into constructing a working model of a design from a schematic, not to mention the hours and days required for troubleshooting the one elusive misplaced wire or having to start over because of an unexpected smoke/fire.
We have come a long way over the past 30 years of moving designs through the prototype stages. Instead of pen and paper and wire and breadboards, we now turn to our computer screens where the engineer can design a circuit, construct a layout, perform circuit analysis and order prototypes in days and weeks instead of months.
Today, we will navigate further into the prototype world, the things you need to know about quick turn assembly houses and how to choose the right one for you.
Where To Start?
If you search the web for electronic prototype houses you will get plenty of options. What works best for you can start out as a personal choice, but in the end you, the engineer, are looking for accuracy, delivery, and convenience. Price may play a part in your decision, but you will usually get what you pay for.
Working local is ideal because you can easily visit to see if it is a legitimate shop and determine whether the proprietors are interested in giving you their attention. If you are going through a website, it is wise to pick up the phone and talk to a rep. Are they courteous? Knowledgeable? Do they ask questions and offer suggestions regarding your project build? Unfortunately, in the end you won’t know for sure until you use their services at least once.
Components
Many engineers (myself included) believe we can do things better. However, I have seen enough of the component procurement process to know that any money saved in parts bought for a consigned kit will be more than offset in the assembly difficulty on the house’s side and could result in a compromised delivery.
What we do not see at the assembly house is that in order to process your assembly efficiently and completely, some rules have to be followed. The 3” strip of 0402’s you paid $.35 for, could cost you $7.00 in increased assembly cost and/or a delay in the build. Even the best SMT machines will deal in feeder issues such as: setup fallout, placement fallout, tape advancement, lack of leader tape, etc. If at all possible, let the assembly house buy the parts. They have the resources and contacts to find what you need because they do this every day. It is much easier to let the house work for you. One, you don’t have to do it, and two, they’re responsible for the right parts, not you. You will pay a markup for the parts, but someone has to put in the time to buy them. Remember, your time is money too.
Soldering Complexities
As engineers, we pride ourselves in our ability to theorize and apply knowledge to create something that has purpose and functionality. That’s the hard part. Soldering components on the board? Piece of cake, right? Well, maybe not.
Let’s talk sheet rock. Anybody who has looked at their unfinished basement and pondered the possibilities of a remodel, and then went forward with the implementation, knows what I am talking about. Laying out the space? Check. Hanging sheet rock? Heavy, but manageable. Mudding the walls for a smooth, finished look? Uh……
Today’s electronic assemblies consist of components that cannot be seen without magnification and IC’s with invisible terminals. Soldering something you can’t see is not a long term career move. Modern electronics assemblers possess precise assembly equipment for a reason, humans just can’t do it. Bottom-side termination BGAs or pepper-size 01005 chips must be assembled and soldered by machines designed for just that purpose. Reflow ovens with multiple heat zones are designed to operate to specific temperature profiles so as to ensure proper solder joints. Convection reflow is probably the most common method of reflow used today. However, as IC’s become larger and more sensitive, and surrounding components become smaller and more delicate, other means of heat applications, such as vapor phase reflow, may need to be incorporated. A house having multiple reflow options gives you flexibility for your project.
In today’s world, a PWB with big-massed BGA’s + small delicate IC’s + standard convection reflow = toast the one, insufficient solder on the other. I’m not saying convection wouldn’t work, you just need to make sure the assembly house has a good handle on it and how it applies to your project. Vapor Phase, however, simplifies things. It minimizes over-temp because the oven temp never extends beyond liquidous, and maximizes mass loading of the oven because the component mass does not play as critical a role in soldering.
Beyond SMT reflow there are many different ways assembly houses can solder the remaining components. Anywhere from hand soldering to robotic and wave soldering will give you an ideal blend of accuracy and expediency. Knowing this plays into how your project will be manufactured on a production scale. It would be nice to know up front that your project can be built on standard equipment vs finding out later you have to purchase $30k in NRE tooling because you decided to get “creative” with your design.
Delivery and Speed vs Cost and Accuracy
Most assembly houses will quote you a delivery time. The shorter the delivery the higher the price, and the cost is not linear but exponential as the time gets shorter. I understand the pressure engineers are under in trying to perfect the design prior to prototype. A lot of engineers will use almost all the available time to design, and then pay the proto house a truckload of money for a 24hr turn. You will need to know your assembly house and whether any corners are cut in order to turn something in 24hrs. At the end of the day, you need a working unit and that’s all that really counts. I will take a day or two late on my deadline over asking for more money for a do-over because of an oversite due to rushing to be on time.
Final Notes
Remember, the only goal in this entire process is to prove your design works with a working model.
Choosing a proto house you can trust, one that takes the time to understand your specific project requires some time and research. If at all possible, visit the facility to get a good feel for where you are spending your money. If you can’t visit, talk to the rep. You can glean a lot from a conversation in how you are treated and how they respond to your questions at the very beginning. Word of mouth from your engineering buddies is a great way to avoid the mistakes of others.
It’s not rocket science, it’s harder. Sourcing and finding the right vendor is not exactly in an engineer’s wheelhouse. However, once you get past the initial contact phase and find a vendor who meets your needs, you can get on with the important stuff, like the free pizza in the break room.
INDUSTRY INSIGHTS
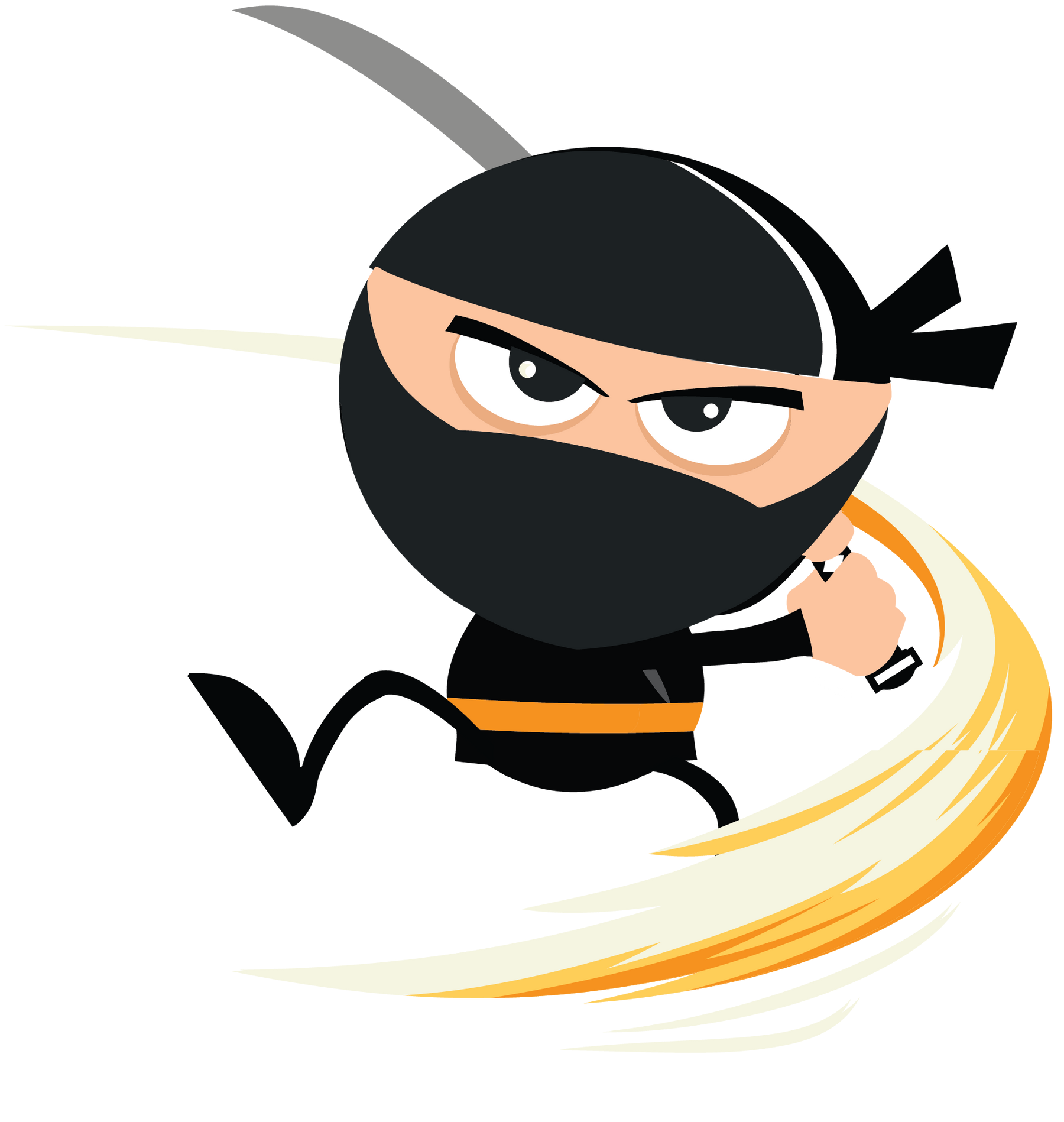